Idehaza aktívan zajlik a negyedik ipari forradalom. Igaz, sokan már az ötödikről diskurálnak, de tapasztalataink alapján temérdek gyártó eddig még csak a harmadik vívmányait integrálta sikeresen. Ez a téma is megérne egy elemzést, de most inkább maradjunk egy olyan témánál, amely mindeddig valamennyi ipari forradalom technológiai innovációinak közös célja volt: ez pedig
a hatékonyság(fokozás).
Kevesebb ráfordítás, magasabb profit
Ki ne szeretne kevesebb ráfordítással többet gyártani, és a nap végén magasabb profitot realizálni? Hogy a hatékonyságot miként lehet fokozni, az rendkívül kontextusfüggő. Egy biztos, a veszteségcsökkentés a termelésben iparágtól, gyártási technológiától függetlenül is közös kihívása a termelésnek.
Veszteségcsökkentés
Első lépésben a problémát érdemes azonosítani, ami számunkra a veszteséget jelenti. Előfordulhat, hogy nem tudjuk mi az, és pont ennek feltárása szeretnénk egy rendszert bevezetni. Ördögi kör. Most akkor honnan is kezdjünk hozzá?
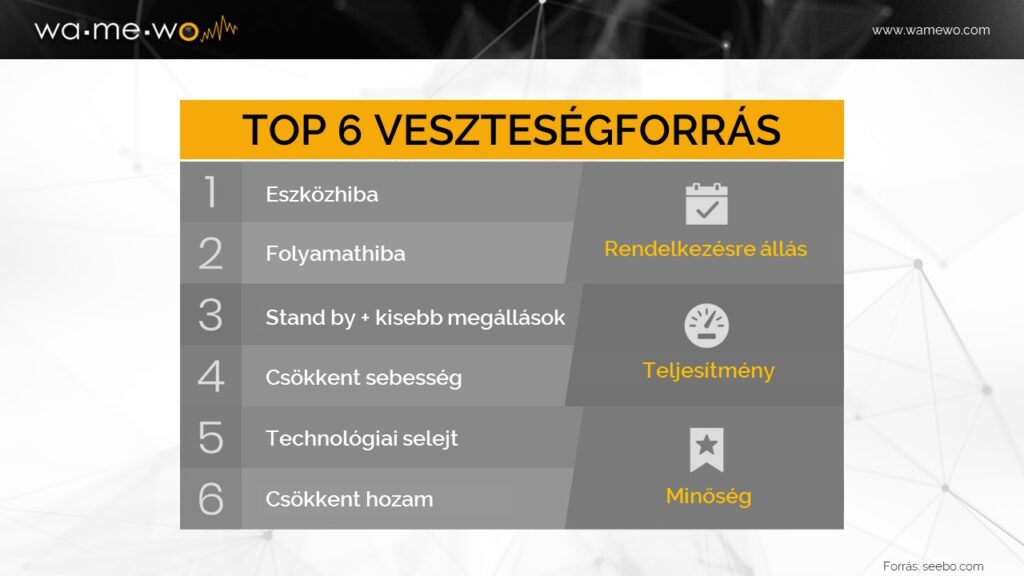
Van egy jó hírünk: különböző statisztikák érhetőek el a nagyvilágban arról, hogy a gyártók háza táján mik a legnagyobb (ismert) veszteségforrások. Egy ilyen felmérést tett közzé korábban a seebo.com is, amely szerint, ha az OEE (az OEE bugyrait egy későbbi fejezetben még részletesen kivesézzük) argumentumai alapján azonosítjuk a veszteségtípusokat, akkor egyértelműen a berendezések nem elégséges rendelkezésre állása okozza a legtöbb felesleges költséget. És mikor nem áll rendelkezésre egy gép? Amikor valamilyen anomália miatt áll. Meg is érkeztünk a témánkhoz:
Mit kezdjünk az állásidőkkel?
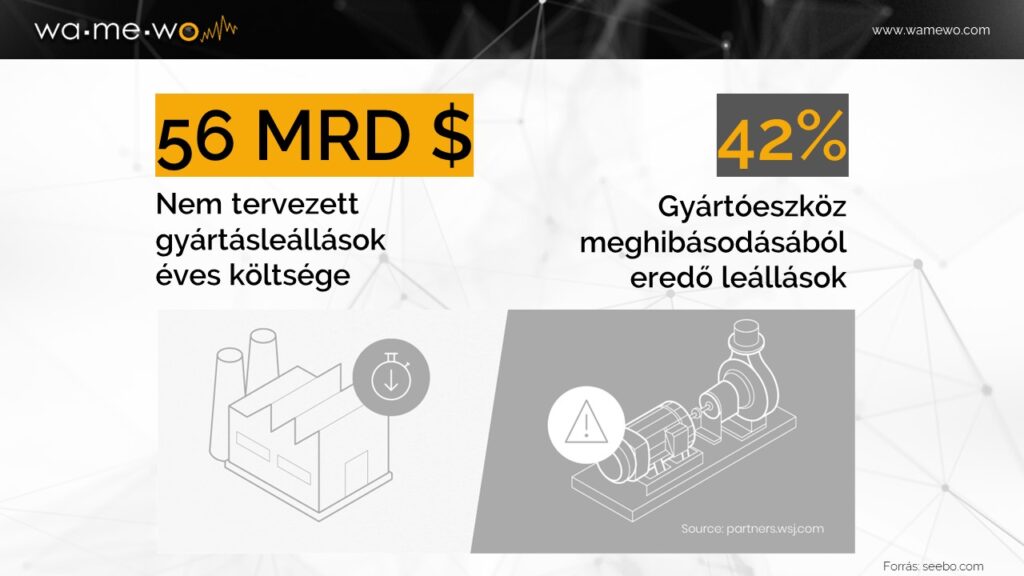
A válasz lehetne nagyon rövid is: számoljuk fel, szüntessük meg. Rendben, de hogyan? Hol avatkozzunk be? Mit csináljunk?
Ha felkeressük az interneten a különböző ipar 4.0, digitalizációs és IoT szoftveres megoldásszállítókat, majdnem mindenki igyekszik a veszteségcsökkentés kérdéseire választ nyújtó rendszereket ígérni. A legbátrabbak AI/ML alapú anomáliapredikciót is kínálnak, amely képes lehet előre jelezni, ha valamilyen gépen megállás várható, amihez aztán a szükséges karbantartási intézkedéseket ütemezhetjük.
De mégis hogyan képes egy algoritmus a „jövőbe látni”? Ahogyan a humán prognózisok is készülnek: a múlt tapasztalatain alapulva. Tehát, ha szeretnénk egy ilyen intelligens jóst az üzemünkbe, akkor előbb el kell neki mesélnünk, mi is történt a múltban (minél többet és minél részletesen, annál jobb), hogy az így felcímkézett mintákat megtanulva felismerje a jelenben a nem kívánatos leendő események előjeleit – mégpedig még időben. Legyünk tisztában a valós lehetőségekkel: ezeknek az algoritmusoknak rengeteg „előválogatott” bemeneti adat kell.
Jelölnünk kell, melyek a nem kívánatos korrelációk, az algoritmusok fejlesztése speciális tudást igényel az adattudósoktól, a modellek (folyamatos) betanítása pedig nagy számítási kapacitást kíván.
Ma a gyártók jelentős hányadánál a gépek megállásának okait még papíron rögzítik a műszak végén, amelyet aztán valaki begépel egy Excel táblába, majd egy másik személy pedig kielemzi azt és megmondja, hogy két hete azért nem tudnak eleget gyártani, mert túl sokat áll a gyártósor amiatt, hogy… Így viszont egyrészt két hétig veszteségesen gyártott a cég, terhelte a környezetet a papírokkal, másrészt a kreatív emberi szürkeállományt monoton, adminisztratív feladatokra használta. Rengeteg veszteség éri a vállatot, mire így feltárják a probléma forrását.
Mi lenne, ha azt mondanánk, hogy a papír alapú adatrögzítés és a futurisztikusnak ható mesterséges intelligencia közé kínálunk egy olyan belépési pontot, amely egyszerre számolja fel múlt hiányosságait és ágyaz meg az adat alapú termelésirányításnak?
A WaMeWo beépített „Állásidők” és „Állásidő riportok” funkciója pontosan ebben segít. Nézzük meg részletesebben, hogyan is működik!
A rendelkezésre állás fokozásához három információt kell feltálalnunk, hogy azok érdemben (ember vagy gép által) elemezhetővé váljanak:
- mikor és milyen hosszú leállások következtek be,
- milyen, a gépekből gyűjtött hibák válthatták ki azt,
- a leálláshoz milyen magyarázatot fűz hozzá az operátor/technikus.
Teendők gépleállás esetén
#1 Állás detektálása
Először is arra kell módszert kidolgoznunk, hogy teljesen automatizált módon detektálni tudjuk a berendezés azon üzemállapotát, amikor az áll(t). A gépek vezérlőiből gyűjtött adatok alapján ez többnyire könnyedén megállapítható, és kinevezhető egy ún. flag, amely egyértelműen jelzi, hogy hiba miatt állt meg a gyártás.
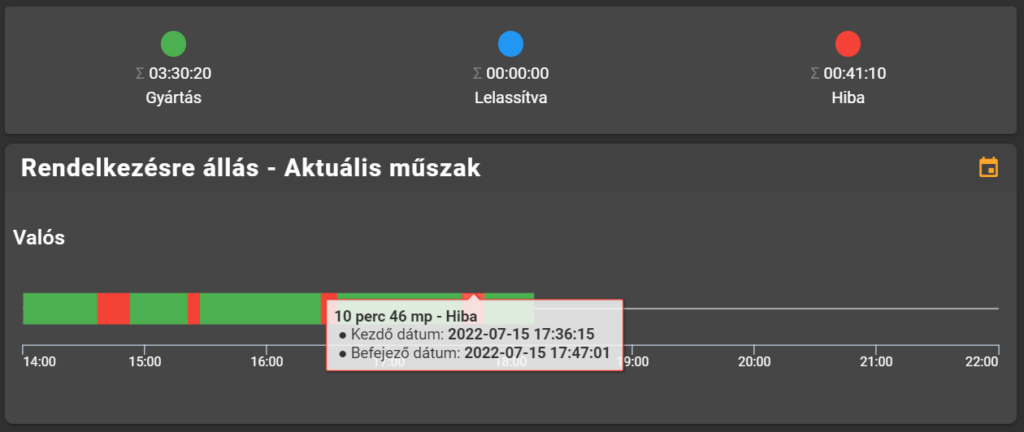
#2 Állásindok megadása
Már tudjuk, mikor és mennyi ideig állt a gépünk, de azt még nem, hogy miért. Előbb érdemes azt a kérdést is feltennünk, hogy milyen hosszúságú az az állás, amivel érdemes foglalkoznunk. Persze erre mondhatnánk, hogy mindegyik, de például egy 30 perces ciklusidővel működő gyártási folyamatnál nem biztos, hogy érdemes a másodperces mikroleállásokat vizsgálni mindaddig, amíg a hosszabbakat nem számoltuk fel. Ha megvan a bűvös érték, amire első körben méretezni szeretnénk, akkor a WaMeWo-ban egyszerű paraméterként megadhatjuk, milyen hosszú állásidők esetén kérjünk indoklást a külvilágtól, hogy mi okozta azt. Ha ez bekövetkezik, akkor például egy előre definiált listából adhatja meg az operátor egy intuitív felületen villámgyorsan az állást kiváltó okot…
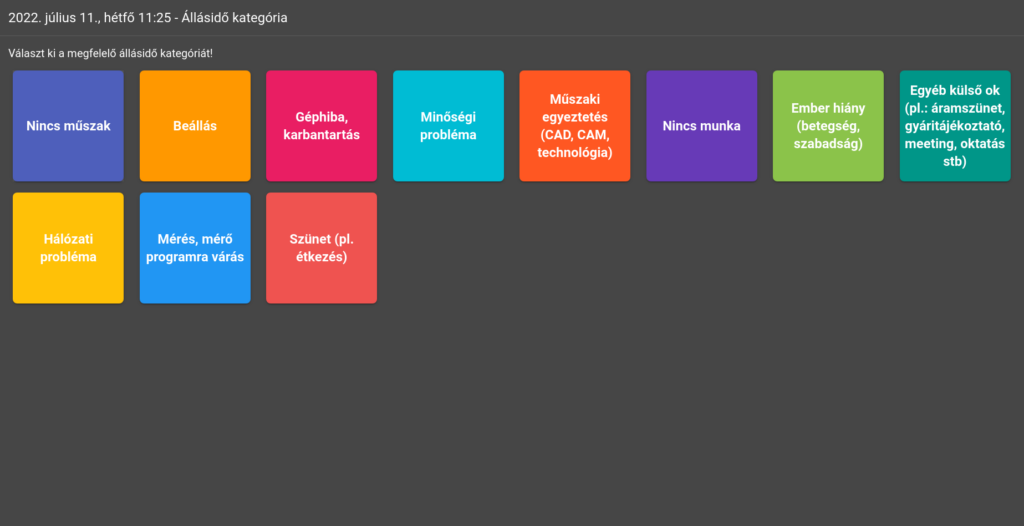
… de akár hisztorikusan is elérheti azokat.
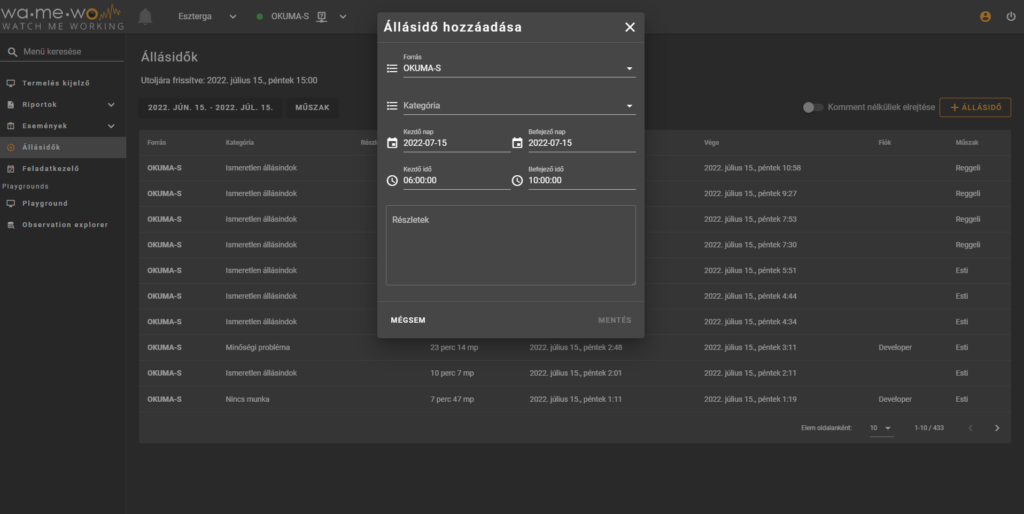
Hitvallásunk, hogy minden információt lehetőség szerint a gépektől gyűjtsünk be, de vannak esetek, amikor még szükséges az emberi visszacsatolás. Ilyen eszközökkel nagymértékben fokozható a digitalizáció (megspóroltuk a papírt és az Excelt), valamint sokkal jobban előkészített adatbázisunk áll majd rendelkezésre egy tanuló algoritmus számára is akár.
#3 Állások elemzése
Ha még mindig egy Excel táblát használnánk, akkor az összegyűjtött állások valamilyen preferenciájú kielemzésére saját kimutatást kellene készítenünk. Legdivatosabb ilyen preferencia persze az, hogy mi miatt állt legtovább, vagy legtöbbször a gyártásunk. A WaMeWo beépített statisztikai modulja erre rögtön választ ad, csupán át kell kattintanunk a megfelelő menübe. Itt akár egész gyárra, területre, gépre fókuszálva vizsgálhatjuk az okokat, vagy szűrhetünk rá egy keresett állásindokra.
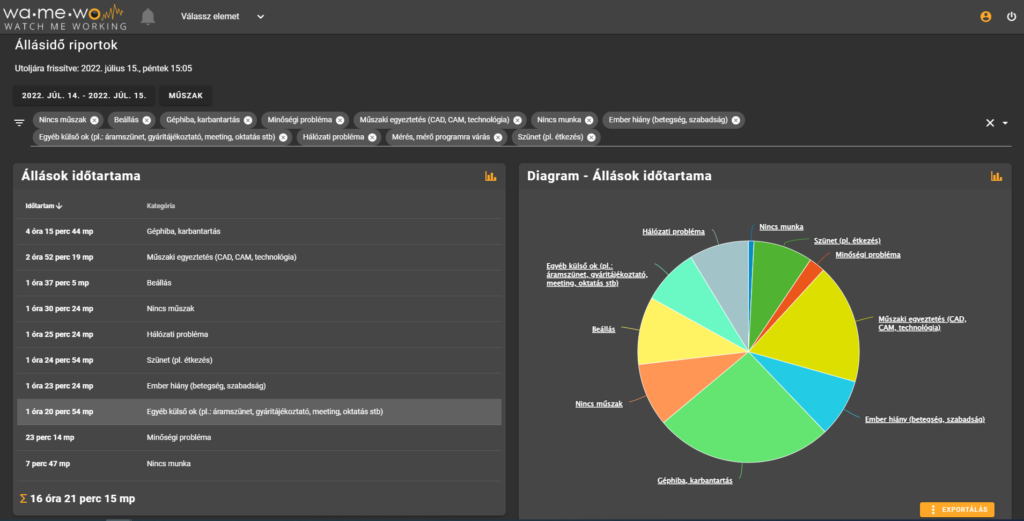
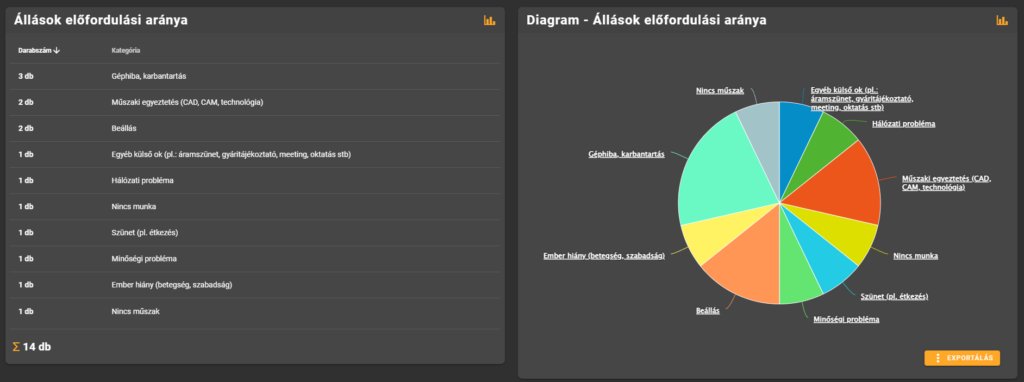
#4 Összefűzés gépi hibákkal
És ez még nem minden. A gépi adatok hitelességét se hagyjuk veszni, így a WaMeWo „Állásidők” menüjében nemcsak, hogy felsoroljuk a leállásokat és azokhoz indokokat fűzhetünk, hanem arra is kidolgoztunk egy eljárást, miként korrelálhatjuk mindezt a berendezés saját hibaüzeneteivel. Amennyiben a gép vezérlőjéből elérhetőek a saját rendszerüzenetei, úgy azokat (egy külön funkcionalitásban) gyűjtjük és elemezzük. Miért is ne kapcsolnánk össze a leállásokkal!?
A szolgáltatás a detektált állást megelőző egy perctől indulóan, az állás végdátumáig tartó hibákat kilistázza. Ennek köszönhetően jó eséllyel a listában lesz a hibaüzenet is, amely összefüggést mutathat a leállással. Remek táptalaj ez egy komplexebb algoritmus számára a továbbiakban.
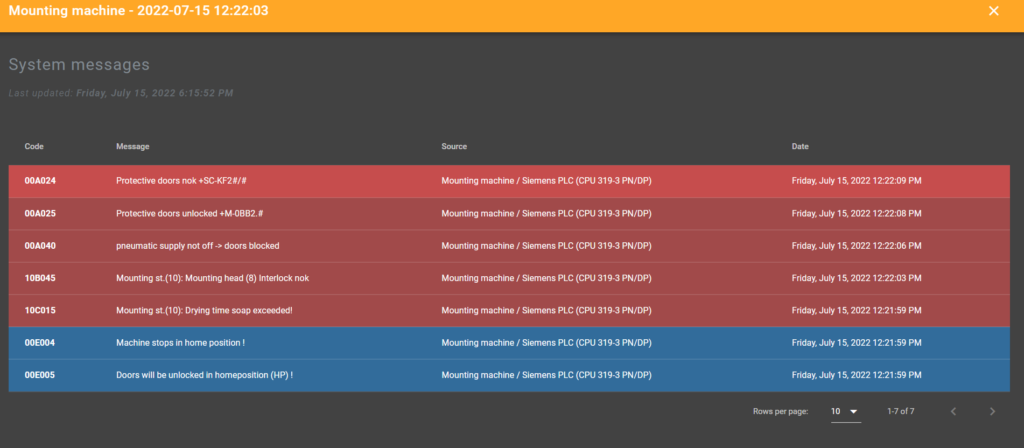
Útravaló
A fenti esettanulmány tipikusan a digitalizációs eszközeink egyik legkeresettebb portékája, amely ugyan nem ígér utópisztikus elemzési eljárásokat, viszont pont ott segít a legtöbbet, ahol leginkább szorít a cipő:
- még inkább papírmentessé teszi az üzemi területet,
- hisztorikus adatokon alapulóan könnyedén elemezhetővé teszi a kiváltó okokat,
- a jövőre gondolva segít mielőbb “megágyazni” egy leendő mesterséges intelligenciának, amely egy következő lépésben már megoldási lehetőségeket kínál majd számunkra – amennyiben arra is megtanítottuk.
Miről szól ez a cikksorozat?
Cikksorozatunkat szakmai- és üzleti know-how szomjoltásra egyaránt ajánljuk az ipari szektor digitalizációjával foglalkozó szakemberei számára. A fejezetek tartalmának összeállításakor két vezérelvünk volt:
- feltárni a felhasznált gyártásdigitalizációs szoftvertechnológiák miértjeit
- és bemutatni azok üzleti hasznosulásának lehetőségeit.
Bízunk benne, hogy tartalmaink építő szakmai diskurzust váltanak ki. Az info@indeveyes.com-on vagy közösségi felületeinken örömmel veszünk visszajelzést, véleményt, vagy kérdéseket a témával kapcsolatban!
- A sorozat előző cikkében a A gépi adatgyűjtés legfontosabb kritériumai-ról írtunk.
- Következő cikkünkben az OEE-mérésekről lesz szó.