“Lack of planned maintenance is planning for future failure.” (unknown author)
Well-organised maintenance activities are one of the cornerstones of efficient manufacturing operations. Unplanned downtime and unexpected breakdowns
- can also disrupt the production process,
- and generate significant costs,
- with a negative impact on all production performance indicators.
This is why the digitalisation of maintenance processes has become a focus of production optimisation in recent years.
Maintenance managament in the past and present
Maintenance strategies have evolved significantly in parallel with industrial development. The initial “operate until failure” approach has been replaced by planned preventive maintenance and then by reliability-centric thinking. Digitalisation, which was the forerunner of the fourth industrial revolution, gave a new impetus to this field, creating data-driven predictive and prescriptive maintenance methods.
The initial versions of CMMS (Computerised Maintenance Management System) systems focused primarily on digitising administration. These systems documented maintenance activities but did not provide real-time data and analysis capabilities.
The objective of the next generation of maintenance management tools goes beyond this: they are tightly integrated with production control systems and support decision-making based on real-time data.
Data-based maintenance managament in practice
Data-based maintenance management systems can manage three main types of maintenance:
- Corrective Maintenance (CM): quick and efficient remediation of faults that have already occurred
- Preventive Maintenance (PM): the execution of scheduled, planned maintenance tasks
- Predictive Maintenance (PdM): interventions based on condition monitoring
[NOTE] Often the optimal combination of maintenance strategies will ensure the best results. For critical equipment, a predictive approach may be appropriate, while for lower priority assets, a preventive or even troubleshooting approach may be appropriate.
How do we deal with errors effectively?
One of the key elements of modern maintenance management systems is a structured defect management process that supports the following process steps:
- Fault reporting: user-friendly interface, minimal data entry, documentation facilities
- Prioritization: automatic or manual prioritization with minimal user input and easy accessibility
- Resource allocation: provision of appropriate staff and tools
- Implementation and documentation: detailed recording of the intervention
- Analysis: systematisation and evaluation of failures and solutions
The efficiency of the defect reporting and management process is significantly enhanced by the user-friendly mobile device support, which allows for immediate, on-the-spot documentation and tracking of defects.
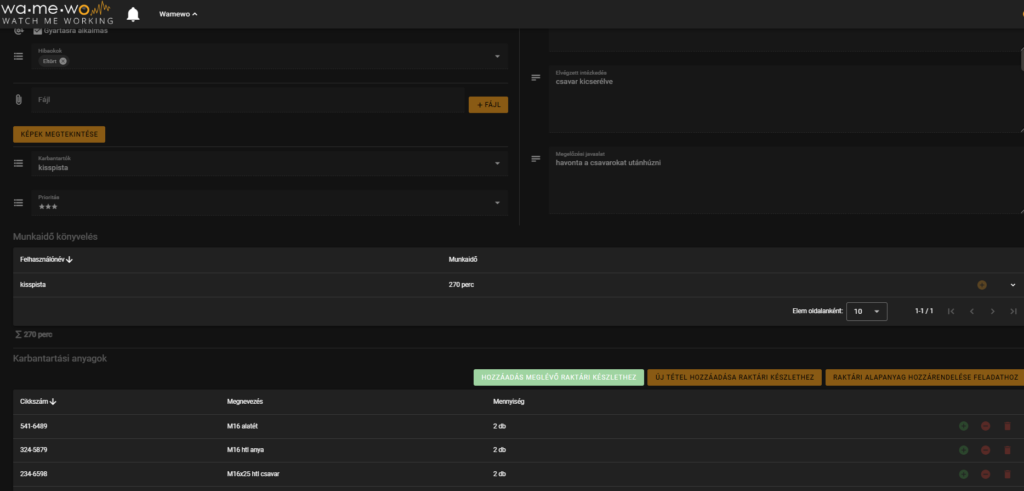
What is wrong with the under-appreciation of knowledge management in maintenance?
Retaining and transferring the professional knowledge that accumulates in manufacturing plants is a critical challenge. As experienced maintenance professionals retire, significant expertise can be lost. One of the most valuable functions of digital maintenance management systems is to create and develop a knowledge base and make it available in a user-friendly way.
[NOTE] When uploading maintenance documentation, we advise our customers to capture not only manufacturer documents but also “best practice” descriptions within the organisation in a structured format, using a consistent tagging system for searchability.
What is necessary for an efficient knowledge base?
- Developing document management standards
- Consistent use of metadata
- Ensuring version tracking
- Use of automated document processing (e.g. OCR technology)
A well-structured maintenance knowledge base can significantly reduce training time and increase the efficiency of maintenance operations.
An outstanding capability of the WaMeWo PVM (CMMS module) is its ability to automatically generate preventive maintenance instructions from any format (e.g. print, scan, .doc, .pdf, etc.) of machine manual. This feature significantly reduces the administrative burden and ensures that maintenance staff always have the most up-to-date instructions available in a standard format.
Performance measurement and analysis
Maintenance performance measurement is essential for continuous improvement. WaMeWo PVM automatically calculates the most important key maintenance performance indicators (KPIs):
KPI | DEFINITION | REFERENCE |
MTBF (Mean Time Between Failures) | Average time between two failures | Indicates equipment reliability |
MTTR (Mean Time To Repair) | Average time to repair | An indicator of maintenance effectiveness |
MTTA (Mean Time To Acknowledge) | Average response time | Indicates responsiveness of the maintenance organization |
Total Availability | Total availability | Indicates the operational status of the equipment over the entire observed period |
These indicators not only measure maintenance performance, but also help to identify areas for improvement. KPIs, which are regularly reviewed and analysed, can be used as a basis for targeted actions to fine-tune the maintenance strategy.
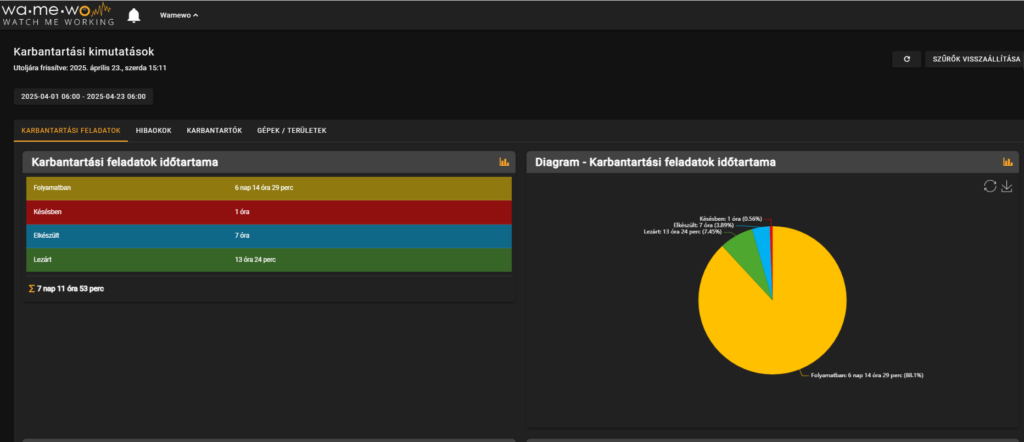
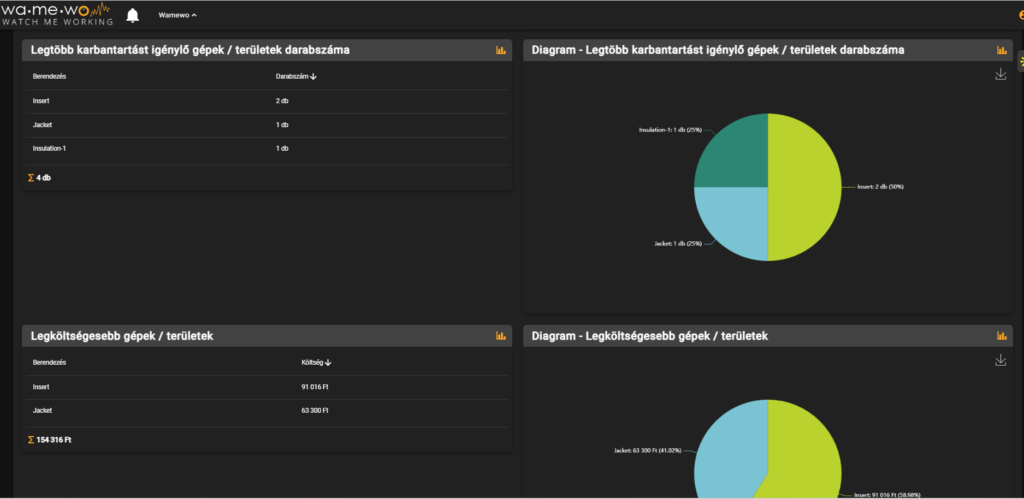
Numbers don’t lie: return on maintenance investments
The implementation of maintenance management systems requires a significant investment, so it is important to make a realistic estimate of the expected return. Let’s look at an example calculation in a typical manufacturing environment.
1. Collect baseline data
PARAMETER | DEFINITION |
Unplanned downtime | Annual downtime due to unexpected breakdowns (hours) |
Production value per hour | Value of products produced per hour of operation (€) |
Average maintenance cost | Parts, labour, other costs (€) |
Maintenance management system cost | Licence fees, implementation, training (€) |
Expected improvement in downtime | Expected reduction after system implementation (%) |
2. ROI calculation
Példa:
PARAMETER | VALUE |
Yearly unplanned downtime | 240 hrs (assuming that 4% of the planned production time [3 shifts x 8 hours x 250 working days = 6000 hours], 240 hrs is unexpected breakdown) |
Production value per hour | 5.000 € |
Annual loss due to downtimes | 1 200 000 € (240 hrs × 5.000 €) |
Expected improvement | Minimum 10% csökkenés a leállási időben |
Expected yearly savings | 120.000 € (1 200 000 € × 0.1) |
WaMeWo PVM yearly costs | ~10 000 € |
ROI = (WaMeWo PVM yearly costs / Yearly savings)
ROI = (10 000 € / 120 000 €) = 0.084
This means that the system can pay for itself in less than a month!
3. Factors that further improve the return on investment
Maintenance cost reduction: more efficient organisation of planned maintenance and optimised use of spare parts will lead to further savings.
Quality improvement: reduced NOK production and less quality problems due to more stable operation can also lead to savings.
Reduced administrative burden: automatic reports and metrics save valuable time for colleagues.
Reduction in inventory value: no need to keep a constant stock of every part of a machine in fear of unexpected breakdowns.
Challenges and best practices in implementing maintenance systems
Implementing digital maintenance management systems can present a number of challenges:
- Organisational resistance: managing natural resistance to change
- Ensuring data quality: the right quality of data is needed for a system to be effective
- Integration difficulties: technical challenges of integrating with existing systems
- Training needs: training users on the new system
[Note] Before implementing a maintenance management system, it is worth assessing your current processes and identifying the main pain points. The system should be selected and configured with a focus on these problems.
Key elements for successful implementation:
- Securing senior management commitment
- Early user involvement
- Gradual roll-out, with pilot projects
- Develop a thorough training programme
- Provide ongoing support
Take away
In the modern manufacturing environment, digitising maintenance management is no longer an option, but a necessity. To remain competitive, it is essential to establish and continuously improve efficient maintenance processes.
A data-driven approach not only reduces costs but also increases equipment availability and lifetime.
Digital maintenance management systems, such as WaMeWo‘s PVM module, provide tools that support all aspects of maintenance strategy, from fault reporting to performance analysis. The flexibility of the system allows adaptation to the company’s specific needs while ensuring standardised processes.
The future of maintenance will evolve towards IoT tools, artificial intelligence and predictive analytics, laying the foundation for fully automated, self-diagnosing and self-healing manufacturing systems.
What is this series of articles about?
This series of articles has been compiled by our team in order to provide both technological and business know-how for professionals involved in the digitalisation of the industrial sector. The chapters follow two guiding principles:
- exploring the reasons behind the manufacturing digitisation software technologies used and
- demonstrating their potential for business use.
We trust that our content will provoke constructive professional discourse. We welcome your feedback, opinions or questions on info@indeveyes.com or our social media platforms!