Why is real-time cost monitoring essential in modern manufacturing?
“Costs do not exist to be calculated. Costs exist to be reduced.”
Taiichi Ohno
How much does one minute of idling actually cost your company? Do you know that today your second shift is 15% more expensive than the first one? Do you notice that there is an 8% difference between the planned and actual cost of producing a new product already in the first week?
Can’t you give an immediate answer to these questions? You are not alone!
Most manufacturing companies still learn about cost trends from monthly or quarterly reports – when it is too late to intervene.
The pitfall of ex-post costing
The biggest shortcoming of traditional cost control systems is that they are retrospective. By the time the finance department produces the monthly report, losses have already been incurred, idle time has been paid for, and overconsumption has been realised. It’s like looking at your bank account at the end of the month – when you can no longer withdraw excess spending.
The cost of invisible losses
In an average manufacturing plant, 15-25% of total costs come from ‘invisible’ losses. These are the costs that:
- do not show up immediately in the statements
- are absorbed into other cost lines
- are not revealed until months later or never reveal themselves
- are constantly eroding profitability
The three main sources of loss that every company should control:
- Idle losses: when machines are running but not producing value. This means not only the cost of energy, but also depreciation, maintenance costs and the opportunity cost of wasted capacity. For a medium sized production line, this can be as much as 10 to 15 thousand euros per minute.
- Efficiency losses. For example, an incorrectly set temperature can increase energy costs by 3-5%.
- Availability problems: unexpected downtime means not only lost production, but also the extra cost of emergency repairs, overtime and the indirect effects of customer dissatisfaction.
Modern manufacturing requires real-time decisions
When a loss occurs, the production manager must be able to recognise it immediately and take action. To do this, he needs real-time production data, or more precisely, the information analysed from it. This is what makes real-time cost monitoring possible.
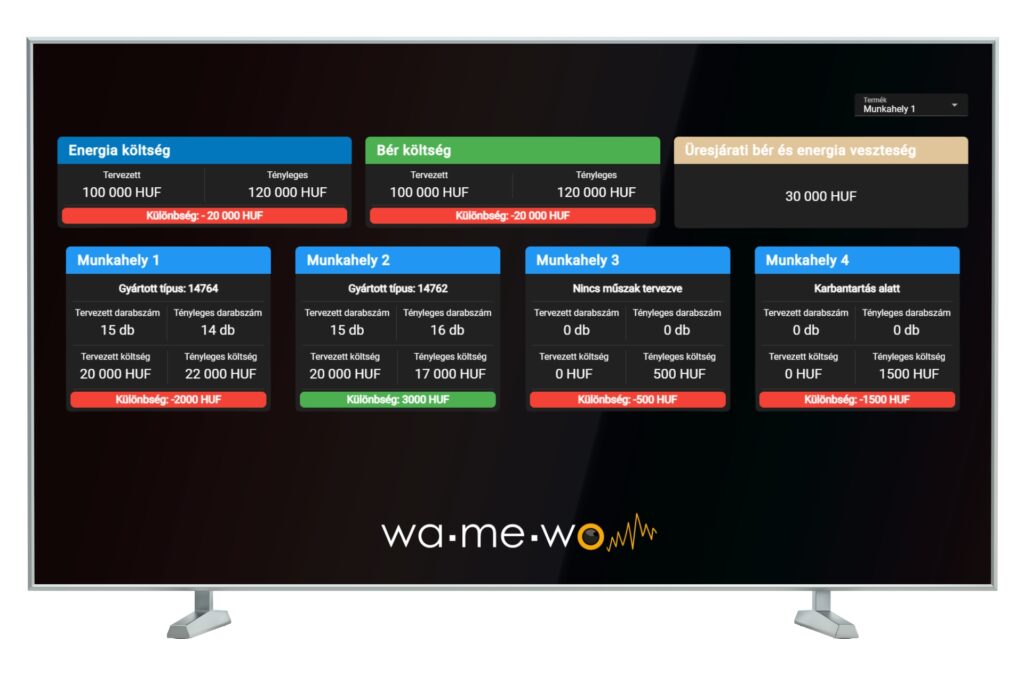
Imagine that not only OEE indicators but also the costs are updated in real time on the production dashboard. Every shutdown, every parameter change is instantly displayed, and in your currency!
Real-time cost monitoring is no longer a utopia, it is now an achievable reality
WaMeWo’s state-of-the-art cost control system can do it:
- integrate data from MES, CMMS, ERP and energy monitoring systems
- calculate direct costs per product, customer, job or production line in real time
- instantly indicate variances between planned and actual costs
- and detect and quantify idle losses.
Take an example of a WaMeWo TCO cost control system implementation!
The WaMeWo TCO (Total Cost of Ownership) module is a complementary component of the OEE (total asset efficiency), NRG (energy monitoring) and PVM (maintenance monitoring) modules, based on their measurement data and complemented by financial controlling metrics. It provides real-time, measurement-based control of production costs, allowing you to keep track of the evolution of margins.
Experiences after the implementation of the system:
End of month #1 | End of month #3 | End of month #6 |
The real-time data showed a striking picture. It turns out that the Friday afternoon shift costs 23% more than the Monday morning shift. The reason: a combination of overtime, Friday idle time and inefficiencies. | Idle time is down 18%. Shift supervisors immediately saw that a 10-minute unjustified stoppage or slowdown costs 150,000. This changed their attitude. | Energy costs were reduced by 12%. The system showed that during the production of certain products, machines were running at 8% higher energy consumption than necessary, and when the machine was not producing, it was idling (kept on standby so that it could produce immediately). |
After six months, the accuracy of new offers has improved by 25%. With the knowledge of the real cost factors, the company was able to set more competitive but still profitable prices.
Creating a cost-conscious culture
The greatest value of real-time cost data lies not in the numbers, but in a change of mindset. When a machine operator sees that an unnecessary idle is costing him £15,000 per minute and that this will be deducted from his moving wage, he will approach his job differently. When the production manager can monitor costs in real time, he will make more proactive decisions.
This transparency leads to a true cost-conscious corporate culture where:
- everyone understands the financial impact of their own work,
- the cost implications of decisions are immediately visible,
- loss reduction becomes a common goal for everyone.
In the current domestic, European and even global competition, only those companies that can grab every penny will survive. But to do that, you need to see those pennies – not at the end of the month, but when you can still make a difference.
Real-time cost monitoring is not a luxury, but a key competitiveness factor. As Taiichi Ohno said: costs are not there to be calculated, but to be reduced. But we can only reduce what we can see – and what we can see when we can still do something about it.
Take-away
Real-time cost monitoring is not just another IT tool in manufacturing, but a paradigm shift in enterprise cost management. With the WaMeWo TCO module, costs become visible and controllable, while there is still room for intervention.
This is one of the greatest promises of digital transformation: not only to analyse after the fact, but also to control processes in real time. In the case of costs, this is particularly critical, as every minute wasted, every suboptimal setting, immediately costs profit.
We can help you make your company’s hidden costs visible and control production costs in real time! Contact us with confidence, because implementing the WaMeWo TCO module can bring you a faster return on investment than you think!
What is this series of articles about?
This series of articles has been compiled by our team in order to provide both technological and business know-how for professionals involved in the digitalisation of the industrial sector. The chapters follow two guiding principles:
- exploring the reasons behind the manufacturing digitisation software technologies used and
- demonstrating their potential for business use.
We trust that our content will provoke constructive professional discourse. We welcome your feedback, opinions or questions on info@indeveyes.com or our social media platforms!