Ebben az írásban röviden bemutatjuk, milyen változásokat hoz(ott) a digitalizáció a minőségügy világába. Az IIoT eszközök révén ma már hatékonyan ellenőrizhetjük, sőt megelőzhetjük a gyártás során bekövetkező hibákat és a selejtképződést. Bemutatjuk az 5 legfontosabb, bevált minőségbiztosítási gyakorlatot, és olyan releváns eseteket is, amelyekben saját gyártásfelügyeleti rendszerünk a minőségi gyártást támogató digitalizációs eszközként is funkcionált.
Miért fontos a minőségbiztosítás?
A megfelelő minőségű termék előállítása minden vállalkozás számára evidens cél. Az ügyfél a kiváló minőségű, váratlan hibáktól mentesen legyártott termékért fizeti ki a teljes vételárat. A gyártást, a kapacitásokat és költségeket is többnyire arra méretezik, hogy e minőségi elvárásnak minden legyártott termék meg fog felelni. Aztán persze a gyakorlatban óhatatlanul „porszem csúszhat a gépezetbe”, és selejt képződhet a gyártás során, ami több fronton is problémát okozhat: alapanyagot pazaroltunk, feleslegesen használtuk az erőforrásainkat (gépek, emberek, energia), raktározási- és adminisztrációs többlet keletkezett, és végül a legvérzőbb seb: az ügyfél is elégedetlenné válhat.
Miért ennyire kritikus tehát a minőségi elvárásoknak megfelelő gyártás? Az elvárt minőségű termékek előállítása során az alábbi szempontokat vesszük általában figyelembe:
- költségmegtakarítás, hatékonyságfokozás (az alapanyag- és erőforrásszükséglet csökkentése, valamint környezeti hatások mérséklése révén)
- több profit
- magasabb ügyfélelégedettség
- tartós üzleti növekedés rövid, közép- és hosszútávon
A minőségbiztosítás tehát minden gyártási környezetben fontos, de például az autóipar (és a nagy pontosságú alkatrész-beszállítók) számára kritikus fontosságú, mivel a magas minőségi színvonal fenntartásának elmulasztása sérülést vagy halált is okozhat.
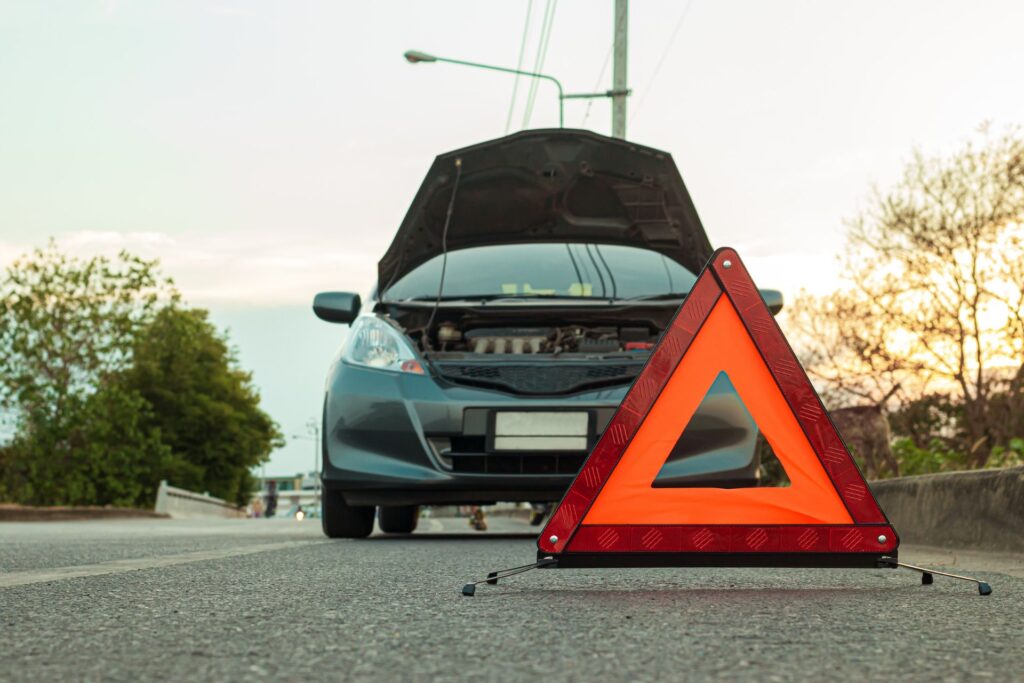
Tiszta vizet a pohárba: minőségbiztosítás vs. minőségellenőrzés
A minőségirányítás egy szigorú módszertan, amelyet a gyártó cégek alkalmaznak termékeik egyenletes minőségének biztosítására. A minőségirányítás két alapvető komponense a minőségbiztosítás (quality assurance – QA) és a minőségellenőrzés (quality check – QC), amelyeket gyakran felcserélnek, de a kettő között fontos különbségek vannak, habár a hatékony minőségirányítási rendszerhez mindkettő szükséges.
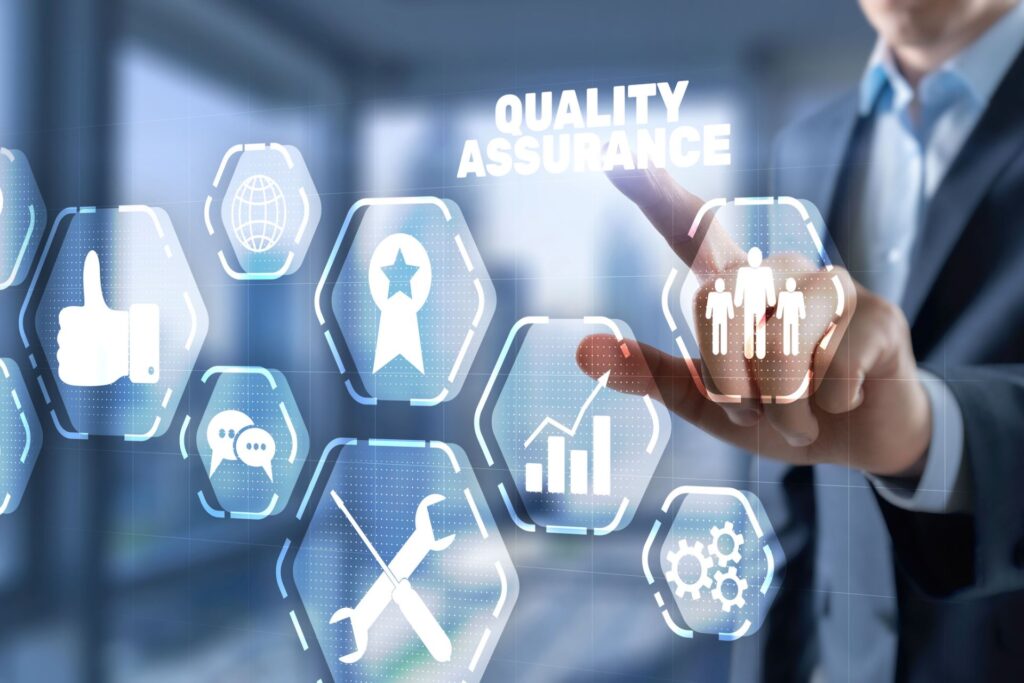
A minőségbiztosítás a minőségi követelmények teljesülésébe vetett törekvések megteremtésére összpontosít (belsőleg a vállalat felé, ügyfelek felé, hatóságok felé). Proaktív elemekből áll: a gyártási folyamatok szabályzása révén igyekszik a nem kívánatos selejtképződést megelőzni, és annak lehetőségét kiiktatni a folyamat minden lépéséből (ide tartozik az auditálás is).
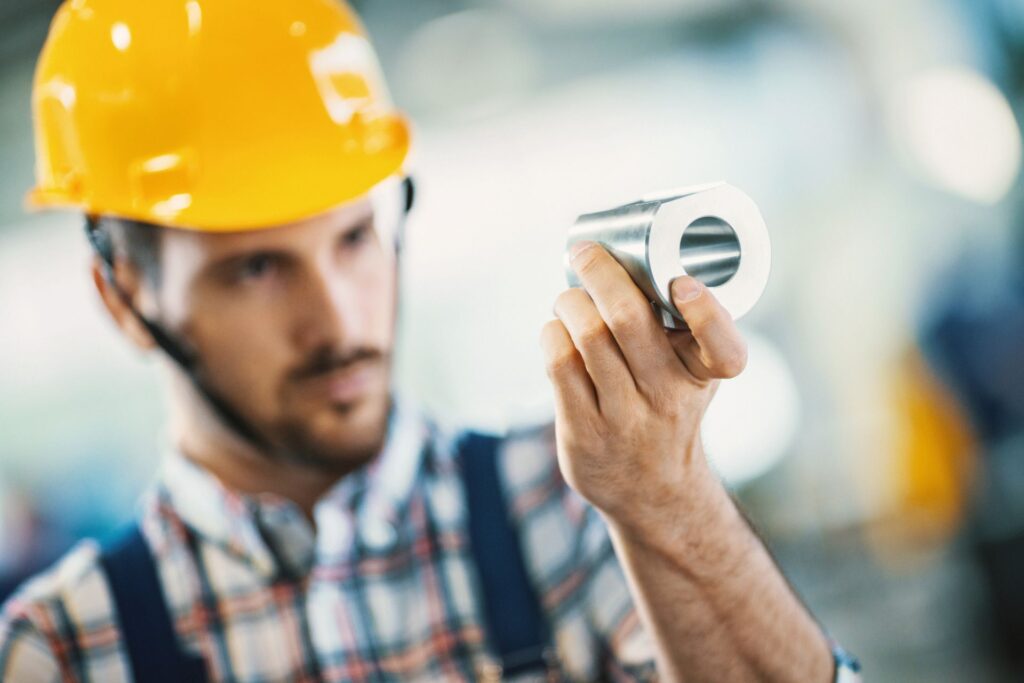
A minőségellenőrzés a minőségbiztosítás egy részhalmaza, és alapvetően reaktív összetevőket tartalmaz, azaz a legyártott termék minőségi jellemzőit méri, de a megfelelőségét nem biztosítja. A minőség-ellenőrzés olyan feladatokat foglal magában, hogy a gyártási folyamat olyan termékeket eredményezzen, amelyek a gyártó által meghatározott, elfogadható konzisztencia szintjén elérik a kívánt minőségi színvonalat.
A minőségbiztosítás legjobb gyakorlatai
Az elvárt gyártási minőség biztosítására ma már több szabvány és módszertan is létezik, ezeket együttesen minőségirányítási rendszernek is szokták nevezni.
A minőségbiztosítás egyes szempontjait például az ISO 9000 szabványosítja, vagy az élelmiszeriparban a HACCP. E szabványok mellett a hatóságok és kormányzati szervek is ösztönzik a gyártókat arra, hogy továbbfejlesszék és alkalmazzák saját belső szabványosítási gyakorlatukat. A következetesség kulcsfontosságú.
A gyártók csökkenthetik a változékonyságot a szabványos működési eljárások (standard operational processes – SOP) használatával, a berendezéseket jó állapotban tarthatják hatékony karbantartási stratégiával (total productive maintenance – TPM), valamint LEAN, 5S vagy 6S stratégiák használatával.
Az 5 legfontosabb, bevált minőségbiztosítási gyakorlat, amit érdemes figyelembe venni:
- A gyártási/szolgáltatási folyamat szabványosítsa és a termékek változékonyságának csökkentse
- Minőségbiztosítási képességekkel rendelkező robosztus MES/ERP rendszer alkalmazása
- Magasabb vevői elégedettség elérése (lojális vásárlók megnyerése)
- Jobb munkafolyamatok kiépítése, melyek csökkentik a költségeket, támogatják a döntéshozatalt, segítik a csapatmunkát
- A hatályos szabványoknak, előírásoknak való megfelelés
Gyártásminőség digitalizációs támogatása
Az alábbiakban néhány olyan releváns esetet mutatunk be, amelyek során a WaMeWo már éles környezetben bizonyított, mint a minőségi gyártást támogató digitalizációs eszköz.
Gyártástechnológia monitorozása 3D modell alapján
Egy autógyári alkalmazásunkban a 3D modelltérben (NX) lokalizált pontszerű kötéstechnológia megfelelőségét hasonlítottuk össze a hegesztőrobotok által elhelyezett ponthegesztésekkel.
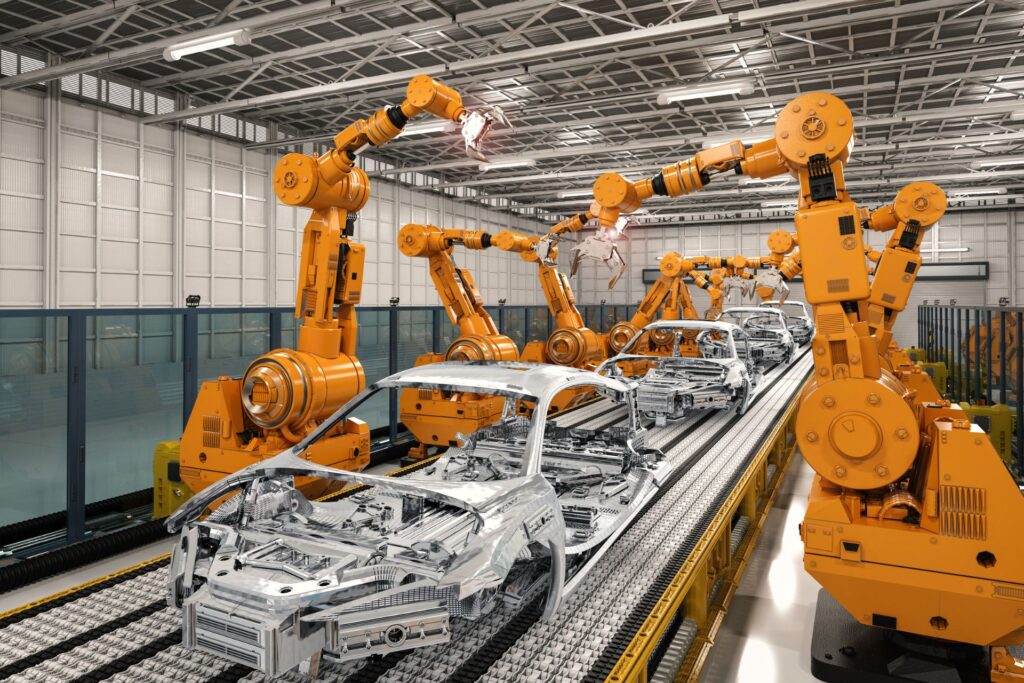
Hogyan működik ez az alkalmazás?
- A letöltött paraméterek és robotprogramok között algoritmusaink megkeresik a technologizálást végző robotpozíciók koordinátáit és egyéb hegesztési paramétereit.
- A kinyert adatokat modern adatbázistechnológiák segítségével eltároljuk.
- Ezzel párhuzamosan a – szintén az adatbázisba importált – 3D pontfelhő koordinátái is előkészítésre és feldolgozásra kerülnek.
- Ezek után egy speciális matematikai transzformáció segítségével a két, egymástól független inerciarendszerű pontfelhőt szoftverünk összeforgatja, és azokon elemzéseket végez. Ennek köszönhetően képesek vagyunk megállapítani, ha a robotprogramból hiányzik egyetlen pont, vagy annak koordinátája vagy bármelyik paramétere eltér a nominálistól.
- Anomáliák esetén a vizualizáció mellett értesíteni tudjuk a feliratkozott felhasználókat a szükséges akciók azonnali elrendelése érdekében.
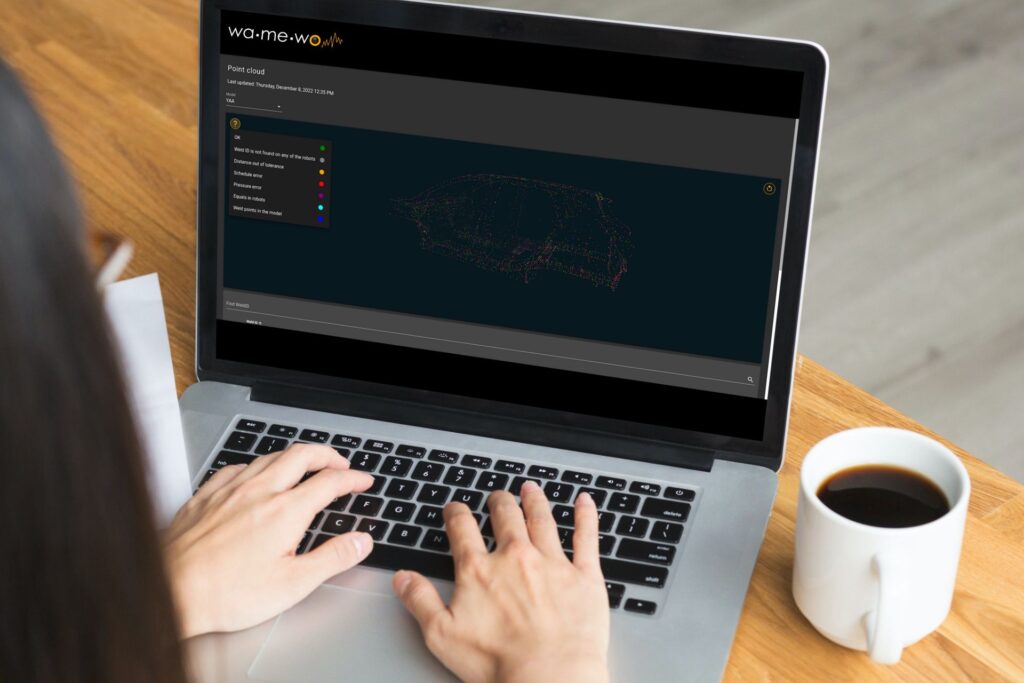
Referenciaértékekhez hasonlítás
Az előzőekben taglalt megoldáshoz nagyon hasonlóan alkalmazható ún. referencia értékekhez, vagy normákhoz történő hasonlítás. Ebben az esetben a gyártástechnológiában részt vevő eszközökről készül a rendszer konfigurálásakor egy „pillanatkép”, amikor is a releváns technológiai információkat (pl. koordináták, nyomásparaméterek, hőmérséklete stb.) elmentjük, és a továbbiakban ugyanezen paraméterek változásait – a gyűjtött adatok alapján – figyeljük. Amennyiben bármelyik eltérést mutat a referenciában megadotthoz képest, arról értesítést és riportokat generálunk.
Technológiai jellemzők monitorozása
A gyártás során alkalmazott technológiák fizikai jellemzőit ma már automatizált aktuátorokkal változtathatjuk a termelés során, programokban tárolt változók segítségével. Így például egy robotkaron lévő festőpisztoly szórásképe szabályozható proporcionális szelepekkel, ragasztóanyagok mennyiségét szabályozhatjuk szervó motorok sebességének állításával vagy ponthegesztések kötésének jellemzőit befolyásolhatjuk szintén szervó nyomatékok vagy áramerősségek segítségével. Megannyi példát lehetne még felsorolni. A mindezekben közös, hogy a kezdeti technologizálás jellemzően időigényes (szimulációk elvégzésével és tapasztalati úton történik), valamint akár programfutás közben is módosítható, így rendkívül fontos annak megelőzése, hogy egy programozási hiba (elírt paraméter) ne okozzon minőségi problémát. Ennek kiküszöbölésére kínálunk olyan funkciókat, amelyek kifejezetten ezeket a paramétereket gyűjtik, figyelik és jelzik változásukat a felhasználók felé.
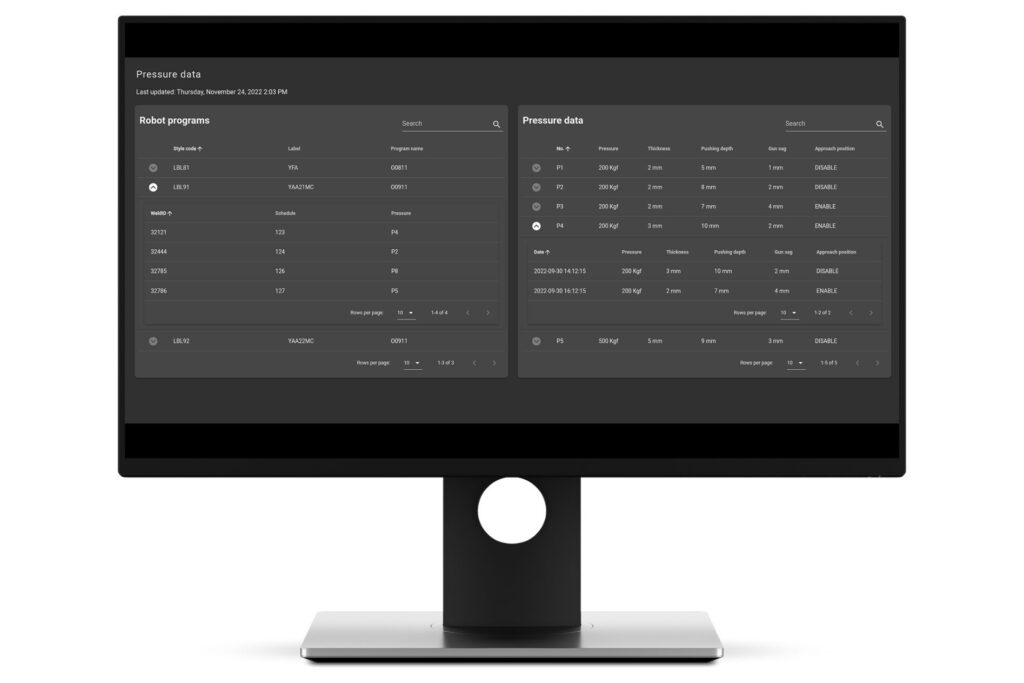
Nyomatékértékek naplózása
Szintén autóipari alkalmazásunkban ügyfelünknél két alkatrész összeszerelését szervómotorokkal hajtott berendezések végzik. Rendkívül fontos, hogy az összeszerelés megfelelő nyomatékkal történjen (megadott intervallumban). Ennek optimalizálására implementáltunk egy olyan megoldást, amely minden egyes legyártott termék nyomatékdiagramját tárolja és vizualizálja, így a későbbiekben bármilyen minőségi probléma, reklamáció esetén termékenként, a WaMeWo felhasználói felületén egyszerűen visszakereshető, milyen nyomatékértékek mellett történt az összeszerelés.
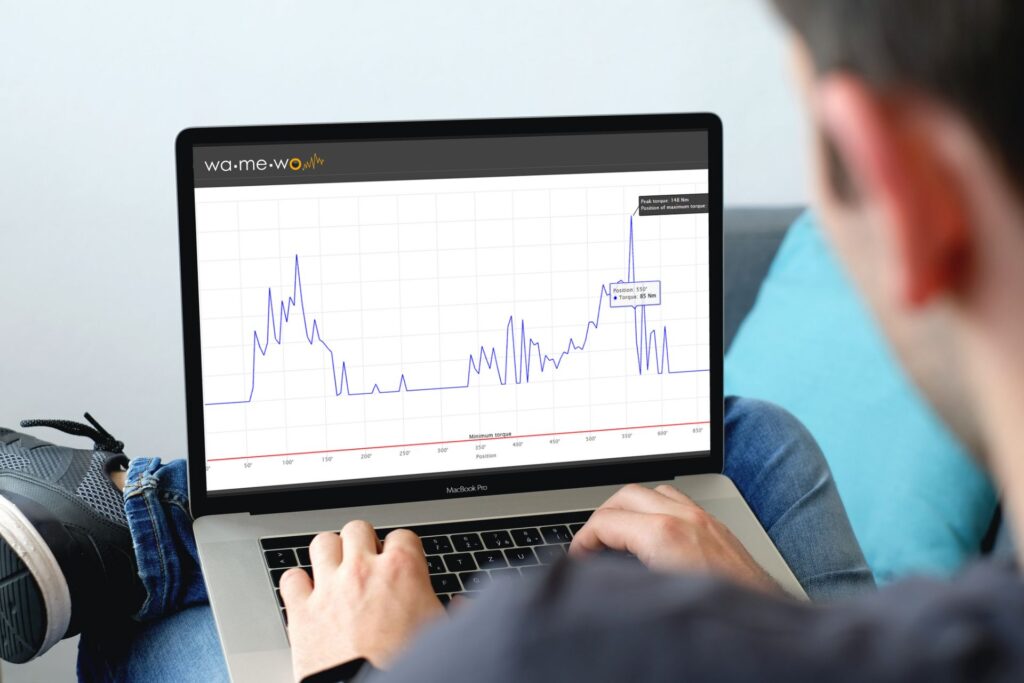
Útravaló
Habár a statisztikák szerint (lásd korábbi bejegyzésünkben) a gyárak TOP 6 veszteségforrásai között a minőségi problémák az utolsó helyeken kullognak, mégis kiemelten kell velük foglalkozni. Egy-egy termék gyártástechnologizálása során a selejtképződés lehetőségének kiiktatása idejekorán megtörténik, ezért jellemzően nem számottevő az ebből fakadó kiesés. Mégis érdemes újra és újra revízionálni folyamatainkat, és igyekezni kiszorítani az elenyésző hibákat is. Ebben sokszor egy kiforrott gyártásdigitalizációs eszköz lehet a segítségünkre.
Miről szól ez a cikksorozat?
Cikksorozatunkat szakmai- és üzleti know-how szomjoltásra egyaránt ajánljuk az ipari szektor digitalizációjával foglalkozó szakemberei számára. A fejezetek tartalmának összeállításakor két vezérelvünk volt:
- feltárni a felhasznált gyártásdigitalizációs szoftvertechnológiák miértjeit
- és bemutatni azok üzleti hasznosulásának lehetőségeit.
Bízunk benne, hogy tartalmaink építő szakmai diskurzust váltanak ki. Az info@indeveyes.com-on vagy közösségi felületeinken örömmel veszünk visszajelzést, véleményt, vagy kérdéseket a témával kapcsolatban!
- A sorozat előző cikkében az optimális riasztási szabályokról írtunk.
- Következő cikkünkben a Személyre szabható, no-code dashboardokról lesz szó.